COULD FACEBOOK’S 3D PRINTED VIRTUAL REALITY GLOVES BE ANNOUNCED FOR OCULUS AT CONNECT? - B-AIM PICK
- PAUL HANAPHY
- Sep 15, 2020
- 4 min read
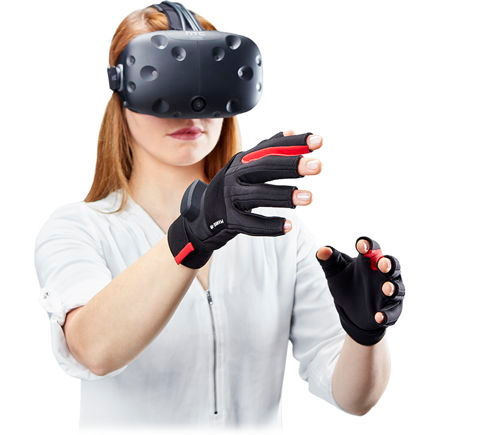
With Facebook Connect 2020 scheduled to take place next week, the firm’s Reality Labs team has announced the development of 3D printed Virtual Reality (VR) gloves.
Created alongside researchers from Cornell University, the devices feature soft pneumatic actuators which “measure localized force” and provide “haptic feedback” for users. Given that Facebook established Reality Labs to oversee the development of VR for its Oculus Rift gaming subsidiary, the 3D printed gloves could yet be part of the upcoming conference.
3D printing soft robotics devices
Devices constructed using soft matter have inherent shock absorbency, load management, and passive energy recapturing advantages over those made using conventional synthetic materials. Soft tissues are particularly useful within robotics, where their low moduli and large extensibility enable the creation of flexible bots that can be deformed into almost any state without breaking.
Silicone rubbers are ideal for creating soft robots due to their thermal resistance qualities and chemical inertness. Despite this, conventional fabrication processes often involve replica or injection molding, which only yields simple, prismatic shapes. Recent rubber research has investigated using liquid silicone materials as inks for extrusion-based 3D printing, but their modified properties have also weakened their crosslinking density.
As a result of the material’s reduced strength, extrusion-based samples have shown limited print fidelity for overhanging features, causing them to slump prior to curing. Other research teams have used stereolithography (SLA) techniques to produce parts with liquid resins, providing greater stability, but not the same toughness as commercially-available rubbers.
What’s more, the processing requirements of SLA demand the use of a stable, low-viscosity resin, which has prevented conventional approaches from being used to strengthen them. As an alternative strategy, the research team hypothesized that creating Double Networks (DNs) wherein two polymers occupy the same volume, would provide a rubber with enhanced strength.
Within the team’s new approach, the two polymeric layers have different qualities and functions. The outer layer is brittle and dissipates energy, while the secondary network remains intact, and is able to sustain heavy loading. Leveraging their DNs, the researchers proposed that they could not just match the strength qualities of commercial rubbers, but also bond the printed objects with other substrates.
The team’s double-silicone 3D printing material
In order to create their new material, the researchers used a thiol-ene silicone formulation as a base due to its low viscosity, rapid gelation, and high reaction conversion qualities. By contrast, the secondary polymer in the DN needs to form its own distinct network, so the team used a Mold Max Series resin due to their inherent toughness and rigidity.
The two-stage combination process saw the rubbers formed sequentially into a photocured thiol-ene silicone and a mechanically robust condensation-cured silicone. Subsequent infrared spectroscopy testing revealed that the relative mass fraction of the two networks could be tuned to adjust the resin’s printability and mechanical performance.
For instance, increasing the loading of the condensation network was found to improve the tensile strength of the final part dramatically, from 0.008 MPa in the ‘green’ part to 0.92 MPa. Leveraging four different tin-based rubber materials, the team then experimented with changing the base material in their DN to adjust its mechanical characteristics.
A similar regime of printable blends emerged, with each having a low enough viscosity to enable SLA 3D printing. The tin-based materials tended to dominate the mix, by providing a higher level of strength, while integrating elastomers provided more customizable performance through different crosslink densities. To demonstrate the applications of their novel polymer network in surgical models, the team later created a hollow 3D printed heart.
Although the cardiac replica was unable to fully replicate the complex mechanical performance of natural tissue, it did possess an elastic modulus similar to that of its biological counterpart. As a result, the joint team’s silicone could be deployed in the future by trainee surgeons for practicing procedures. Combining the flexibility and strength of the DN also allowed the team to create an orthotic glove with four 3D printed pneumatic actuators.
Not only did the device allow for dexterous manipulation, but the bonded structures continued to survive hundreds of movement cycles for more than ten months of usage. According to the team, their glove had proved so robust, that its soft actuators could be integrated into other garments, yielding a new type of wearable soft robotic device.
With Facebook Connect just a week away, the team’s timely advances in soft robotics could yet have a role in the future of VR as well.
Soft robotics and additive manufacturing
In recent years, researchers from a number of institutions have experimented with 3D printing soft robotics, yielding additive innovations in all sorts of shapes and sizes.
A research team from Linköping University, Sweden, has used a custom extrusion-based 3D printer to fabricate a set of microactuators for soft micro robotics. The actuators contain an electrically-active polymer that changes shape once stimulated by an electrical charge.
Scientists from the University of California San Diego have used 3D printing to create flexible, walking “insect-like” robots. The team’s budget-minded production technique is designed to lower the cost of entry to fabricating soft robotics.
Researchers from Zhejiang University of Technology, Tianjin University, Nanjing Institute of Technology, and Ritsumeikan University, have 3D printed a soft robotic finger. The device is operated using an embedded electrode sensor, meaning that it doesn’t require an external power source.
The researchers’ findings are detailed in their paper titled “3D printable tough silicone double networks,” which was published in the Nature Communications journal. The report was co-authored by Thomas J. Wallin, Leif-Erik Simonsen, Wenyang Pan, Kaiyang Wang, Emmanuel Giannelis, Robert F. Shepherd and Yiğit Mengüç.
Nominations for the 2020 3D Printing Industry Awards are still open, let us know who is leading the industry now.
The fourth edition of the 3D Printing Industry Awards Trophy Design Competition is now underway. Enter your design for the chance to win a CraftBot Flow 3D printer.
To stay up to date with the latest 3D printing news, don’t forget to subscribe to the 3D Printing Industry newsletter or follow us on Twitter or liking our page on Facebook.
Are you looking for a job in the additive manufacturing industry? Visit 3D Printing Jobs for a selection of roles in the industry.
Featured image shows soft actuators produced using the research team’s 3D printing material. Image via the nature communications journal.
Watch this video:https://www.youtube.com/watch?v=Z5vxRC8dMvs