Manufacture-Additive Manufacturing: the ultimate game changer for mass production- B-AIM Pick Select
- Kat Plewa
- Oct 5, 2020
- 6 min read
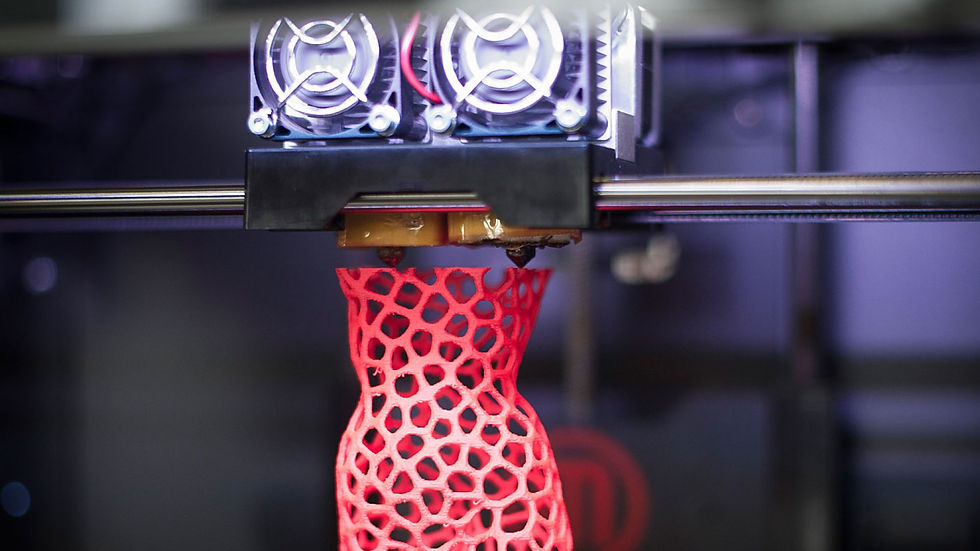
3D printing might seem like a fashionable trend everyone talks about, but the truth is Additive Manufacturing is bringing the new industrial revolution to high volume production. It is highly beneficial for many reasons: it can decrease the costs, speed up the manufacturing process, improve your customer satisfaction and many other reasons. Learn about them all and find out how you can improve your projects and business.
What are the benefits to use Additive Manufacturing for mass production?
Of course! Without a question, 3D printing has numerous benefits for high volume production. We already talked a lot about speeding the production process by miles with 3D printed prototypes, which can be produced in the house, very quickly and are fully capable of performing necessary tests.
But that’s not all 3D printing is about. Additive Manufacturing can actually improve the production in question by providing you with high quality, fully functional end products. There is no reason not to use 3D printing materials for the final products. But there are multiple arguments to do so.
Faster production on demand
In most cases, your products will be manufactured much faster with 3D printing. It is a fact. 3D printers can work constantly and they need very little manual works, it can be even as simple as uploading a 3D file to our online 3D printing service and you can get your parts delivered straight to your doorstep. You can shorten your production time from weeks to literally just days. And that leads to many benefits: the faster you produce your product, the quicker it reaches your customers, it also lowers your manufacturing costs.
Discover design freedom you didn’t know was possible
Other Advantages of 3D printing are the materials, from flexible plastic PEBA to durable metal Titanium 6AI- 4V. Additive Manufacturing gives you a vide variety of choices and totally new design freedom. New materials also mean new mechanical properties. Thanks to 3D printing methods you can create parts with completely innovative solutions to your production needs, such as very complex designs or much lighter parts.
Custom-made like never before
New materials and 3D technologies also give you and your customers an entirely new level of customization. To meet your demanding customers’ needs you have to constantly think of solutions to their problems and come up with innovative products. Additive Manufacturing is just the right answer to that. From fashion to food, we are living in times where made to measure shoes, high-performance gears or 3D printed organs are no longer a vision of imagination, but a reality.
Reach 100% customer satisfaction with 3D printing
With 3D printing, you can also improve your customer service by allowing for much more accessible spare parts. All you need is to have a 3D file designed and you can provide your customers with limitless spare parts- lifetime guarantee. Or you can make it even more efficient by simply sending a 3D file to your customers and they get it 3D printed at their houses or through an online 3D printing service such as Sculpteo.
Additive Manufacturing is the new green
All of those benefits can also come in a sustainable manner. The sad truth is that the industrial revolution from 100 years ago had a huge, negative impact on our environment and it continues to damage the ecosystem. We have to change that. And 3D printing is absolutely capable of that. With Additive Manufacturing methods you will experience less material waste, some materials are already recyclable and we are constantly working on developing new materials.
Stay positive for the environment at a lower cost
3D printing also allows for a fast production of your parts, which means that you don’t have to manufacture more products that you need, risking unselling them and wasting money on storage. On top of all of that, by 3D printing your parts in the house, you don’t need to transport them from subcontractors, which saves time, money and is more eco-friendly.
The best real-life 3D printed projects for high value
Airbus already 3D prints plane parts!
What are you waiting for? One of the biggest fish in the aerospace industry saw the potential in 3D printing for mass production. Thanks to Additive Manufacturing Airbus’ engineers were able to reach a level of design that was unimaginable before, such as elegant, durable and most importantly lightweight natural structures.
https://3dprintingindustry.com/news/airbus-3d-printed-components-to-launch-on-next-uk-satellite-44870/
With 3D technologies their product design has absolutely improved, their 3D printed plane parts are 55% lighter, which results not only in lower cost but also less fuel used for flying which is a real game-changer for Airbus. At the same time, the parts are stronger, which is crucial when it comes to mechanical engineering and the safety of passengers.
Peter Sander, vice president of Emerging Technologies and Concepts for Airbus explains how beneficial is Additive Manufacturing for mass production and explains the process: “In 2017 we will print aluminum parts, in 2018 we will print things like spoilers, and in 2025 maybe an entire fuselage. We are going through the complete aircraft to see where else it makes sense to use 3D printing”.
Using 3D printing for mass production for Airbus also means 90% less energy used and 95% less raw material. The numbers speak for themselves and they make an enormous difference for the production process. It’s not only cheaper but also much more convenient as they can forget about time-consuming tooling and wasted time on assembling the parts.
https://inhabitat.com/airbus-starts-3d-printing-airplane-parts-in-collaboration-with-autodesk-apworks-and-the-living/
https://inhabitat.com/airbus-starts-3d-printing-airplane-parts-in-collaboration-with-autodesk-apworks-and-the-living/
Is the automotive industry behind?
Certainly no! We talked a lot about using 3D printing for prototyping, but Volkswagen noticed the amazing characteristics of Additive Manufacturing and is planning on producing parts for mass production.
Martic Goede, the director of technology planning for Volkswagen, says “A complete vehicle will probably not be manufactured by a 3D printer any time soon, but the number and size of parts from the 3D printer will increase significantly”. Typical car of theirs has up to 8 000 components! Plenty of room to improve their production process with Additive Manufacturing for mass production.
Volkswagen unrevealed that they are planning on using HP metal printing technology. If you’re not very familiar with metal 3D printing, make sure to check out our online metal 3D printing service and technologies such as SLM and DMLS which will prove you with durable and fully functional end products.
https://money.cnn.com/2018/09/11/technology/volkswagen-3d-printing-parts/index.html
And that’s not all. Despite that Volkswagen representative says a 3D printed car is far away future, he might just have been proven wrong by XEV- an Italian manufacturer who collaborated with Polymaker, who was responsible for the R&D.
The most modern car out there is called LSEV and thanks to 3D printing the engineers were able to come up with totally new and innovative product design reducing car parts from 2000 to as little as 57. Not only that, the company achieved a 70% lower cost compared to traditional manufacturing!
And the LSEV is not just a dream or another prototype. It is going into mass production and will be available in April 2019 and it has already reached 7 000 preorders!
Again, the answer is: we are already doing it. It’s no longer a fairy tale that we can combine different materials or create conductive structures thanks to Additive Manufacturing. LITE-ON Mobile Mechanical Strategic Business Group in cooperation with Optomec 3D prints functional electronics such as sensors and antenna patterns onto injection- molded consumer devices. The devices are hybrid plastic/ metal cases strengthen with an embedded metal frame. And the production reaches millions per year! Some of their electronic devices are used for smartphones, tablet components, and covers.
Optomec’s vice president of Marketing, Ken Vartanian explains “LITE-ON did a lot of work to make this breakthrough achievement of 3D-printed electronics in mass production possible. They developed the printing process; for example, modifying the silver ink to lower its sintering temperature below the substrate’s heat deflection temperature. They also developed a pre-printing method to enhance ink adhesion so the printed pattern could withstand stringent environmental testing, such as humidity and salt spray.”
https://www.designnews.com/consumer-electronics/using-3d-printing-mass-production-consumer-electronics/69918448946558?doc_id=280263&print=yes§ion_id=1392
The advantages of 3D printing for Mass production are just massive, don’t wait for your competitors to use them first
With projects like the LSEV cars, where the number of parts was reduced from 2000 to 57 or lightweight and nature-inspired airplane parts for Airbus we can see real-life examples of how beneficial 3D printing is. Indeed, Additive Manufacturing is the future for mass production with the wide range of totally new product design possibilities, faster production, and lower costs. Traditional manufacturing methods simply reached their limits at this point and it is time we start looking at the new, innovative solutions 3D printing methods can give us.
Do you already have an idea on how to improve your production with Additive Manufacturing? Upload your CAD files right now! And if you need any advice, we are also here to help with our design studio, contact us straight away.
And don’t forget to subscribe to our Newsletter and follow our Facebook to stay ahead of your competitors with the latest 3D printing news!