Manufacture-Artificial Intelligence and Robotics in the Manufacturing Industry - B-AIM Pick Selects
- Mario Honrubia
- Oct 7, 2020
- 5 min read
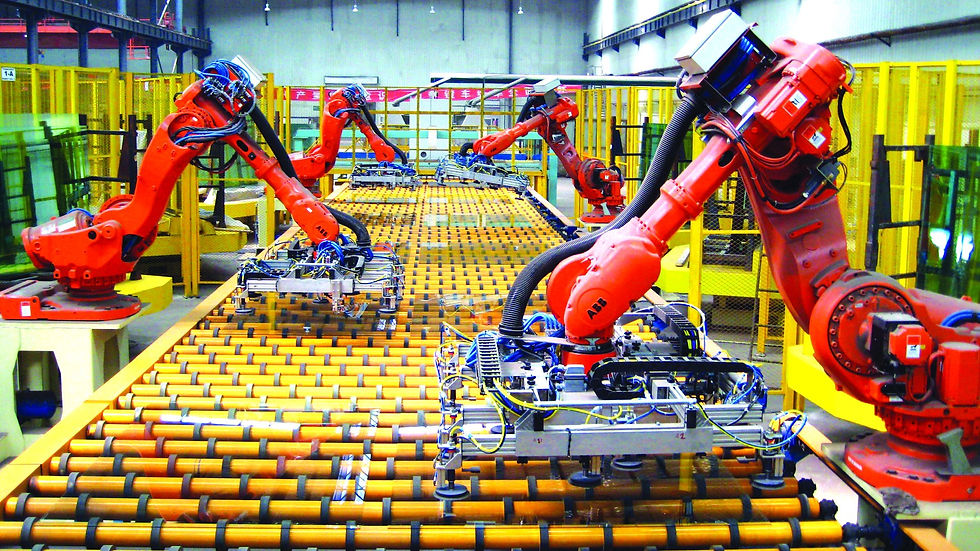
Evolution of the manufacturing industry can be seen with the implementation of Artificial Intelligence and Robotics. This is to minimize the human workforce and, improve efficiency and simplify the whole manufacturing system. Earlier, more than one person was required to manage one task system. With the implementation of AI-based robots, now one bot per task system is sufficient. Here we will see what roles AI and robotics are playing in the manufacturing industry and what are its pros and cons.
AI is the reason behind evolution in the manufacturing industry. They are making production decisions smarter and instant. Nowadays people prefer customized products over costly industrially produced products. With the help of AI, labor cost can be minimized. AI is the next step after robotics for improving productivity and minimization of cost of production. The main causes behind the logical evolution of industries are poor demand and planning, unsafe workplaces i.e. workers are exposed to essential harmful products used in factories, inefficiency, longer and costlier production etc.
Artificial Intelligence is highly essential for the survival and improvement of the industries. Robots play a highly important role in the production, packing, and shipping of products with least manual help.
How essential are Artificial Intelligence and Robotics in the manufacturing industry?
Well, there are certain points which support their use:
Damage Control and Quick Maintenance
With the help of AI-based Robots, detection and solving a fault becomes easier. They are programmed to detect the faults and fed with solutions to overcome the damage.
Automatic Control
Advancement in technology has made it easier for us to control the whole working of a system with the help of just a touch. Artificially Intelligent machines are programmed in such a way that they are able to work automatically and annually depending on the situation. They make accurate decisions.
Demand-based production
Every stage is monitored by sensors, which provide data to AI-based software and production is managed as per the result of data provided. Production is managed depending on the demand and capacity.
Near to Real world
AI-based robots and software are very much near to the real world. They understand and respond to the natural user language as they don’t only study semantic data but also episodic data i.e. from experience.
Work of AI and Robotics in Manufacturing Field
Here are some of the major companies which are contributing to the enhancement of the manufacturing field by investing in machine learning powered approaches. They are Bosch, Intel, Microsoft, General Electric, Siemens etc. Here are the details about how different companies are using this new technology:
Siemens
They use a neural network to keep a check on their steel plant. This has helped them in developing AI for manufacturing purpose. Siemens launched Mindsphere (in beta), which is a smart cloud created to monitor the machine fleets for service purposes.
Their main aim is to monitor, record, and analyze all the processes related from design to recovery. So that they can find fault and correct it within no time.
The biggest achievement of Siemens in the field of AI is the improvement in emission from specific gas turbine better than any other human being. The latest gas turbines have 500 sensors which keep on monitoring temperature, pressure etc. Then this data is fed to their neural network based AI. They are also learning how to acapacity djust fuel valves to create the optimal conditions for combustion based on specific weather conditions and the current state of the equipment.
According to a report provided on the official website of Siemens, researchers have developed a two-armed robot, with the help of artificial intelligence, which can manufacture products without being programmed. The robot’s arms divide the work autonomously and complete the work together as one within less time. The working of the hands was demonstrated at the Siemens Corporate Technology (CT) in Munich, the company’s global research unit. Artificial intelligence has successfully served the purpose of autonomous optimization of gas turbines and monitoring and maintenance of smart grid and other industrial units.
Siemens is using artificial intelligence in industries and making the power grid smarter by providing them with devices to monitor and control the electrical networks.
General Electric (GE)
They have more than 500 factories all over the world and their main aim is to convert them into smart units.
Brilliant Manufacturing suite is a system launched by GE to track and process everything in the manufacturing process resolve the issues and inefficiencies before they emerge. The goal of GE’s Brilliant Manufacturing Suite is to link design, engineering, manufacturing, supply chain, distribution and services into one globally scalable, intelligent system.
According to recent reports, they are working on using drones, crawling robots, AI and predictive analytics to inspect hard-to-reach places. This will enable autonomous optimization and maintenance of industrial units. GE Ventures launched Avitas Systems to take the inspection services industry to a higher level using Artificial Intelligence and robotics.
They are working on a cloud-based system, hosted on GE’s Predix software which will retrieve and analyze data from sensors located on those drones. Unmanned drones, carrying sensors, can easily handle the heat and use infrared cameras and other sensors and help in detecting the problems before their occurrence. These drones will retrieve data and feed it to the Avitas Systems platform. According to the data, the system recommends inspection and maintenance and track changes over time.
Bosch
To attain the most recent technological advancements, Bosch Center for Artificial Intelligence was created in the year 2017. Bosch is working on creating a real-world impact using AI. They are mainly working on the development of six areas using core AI technology. Those six fields are:
AI-based Dynamics Modeling: AI-based modeling of a stationary physical system is already applied while modeling of a dynamic system is still challenging. It is necessary to understand the behavioral and control parameters.
Rich explainable Deep learning: Deep learning is a subfield of machine learning which mainly deals with an algorithm which is very much similar to the structure of the brain. Deep learning is highly beneficial in providing accuracy. More advancement is required in attaining higher perception accuracy and robustness based on various sensors.
Large-scale AI and Deep learning: Development of distributed machine learning and pipeline is required to efficiently make AI effective at large scale. To efficiently explore multi-dimensional hyper-parameter spaces, they are working on techniques.
Environment understanding and Decision making: The main focus is on learning appropriate environment model by constructing a probabilistic generative model using data provided. This helps in decision making and controlling and optimization.
Control Optimization through Reinforcement learning: Since Bosch works mainly in the field of manufacturing, they are trying to find ways to apply AI in production and make it a self-calibrating factory. They are working on transferable knowledge and solutions to decrease set up time and make control structures flexible. This is done in order to enhance the performance.
Dynamic Multi-agent Planning: Autonomous multi-agent system is the driving force in the advancement of industries. Bosch research team is work on creating a strong foundation for dynamic planning and scheduling of robotics fleet.
Bosch is on the verge of transforming its products and services and attracting more customers.
Conclusion
Artificial intelligence and robotics, in collaboration with new technology like 3D printing, will prove beneficial in bringing advancement in manufacturing and fulfilling increasing consumer demands.
B-AIM
Kommentare